Aluminothermic welding is mainly used for the welding of railway tracks. It is a procedure for autogenous welding by fusion using heat produced by the chemical reaction between aluminum and iron oxide, contained in the portion of solder, to melt the rail to be welded (base metal).
The reaction takes place aluminothermic mixing together a part of metallic aluminum with three parts of ferric oxide. The mixture thus obtained (thermite) is placed inside a crucible and triggered by rapid heating. One method is the burning of a strip of magnesium.
The reaction leads to the formation of aluminum oxide and molten metallic iron, given the high temperature (3000 ° C). The aluminum, when it is mixed with iron oxide, in appropriate proportions, easily binds with oxygen. The welding is performed by placing the sides of the rails to be welded of the earth refractory (refractory material) used to create a mold which prevents the flow of molten metal. Once prepared, the crucible containing the reagents is placed above the tracks and proceeds the ignition of the thermite. The enormous development of heat will be such as to melt the parts to be welded thus joining rails into one.
The sealing portion also contains carbon, silicon and manganese to obtain, at the reaction is completed, the right composition of the steel for the rails. In the portion they are inserted also thin disks of soft steel in order to lower the reaction temperature from 2800 to 2100 ° C and to increase the yield. The melting temperature of the steel is in fact of about 1500 ° C.
More information: http://www.heatexchanging.com
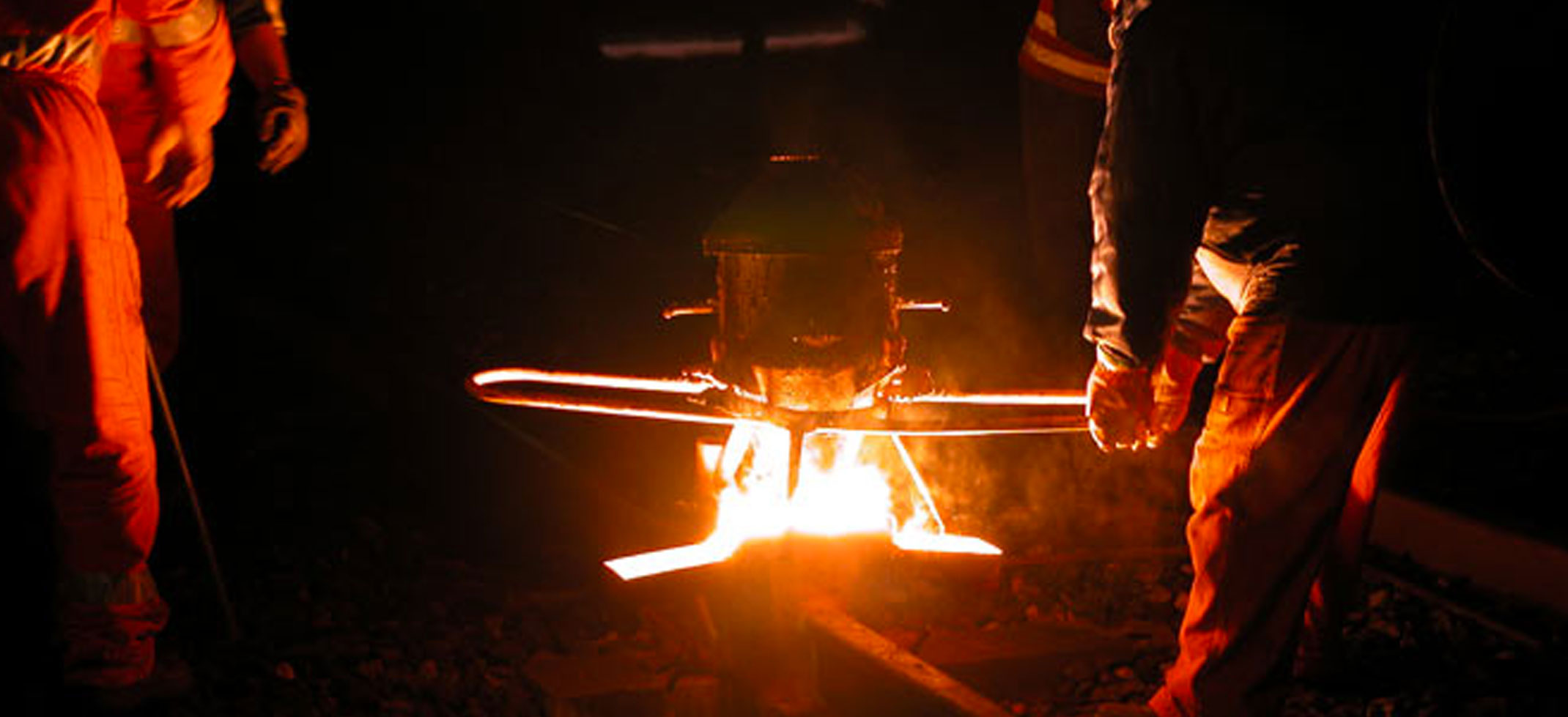