In the past, the tubes were produced by casting in molds, by drilling of cylinders, by welding of curved sheet metal: quite unsatisfactory techniques, because the tubes so made not stand high pressures and were subject to deformation.
Today, with the Mannesmann process seamless tubes can be obtained in iron or semi-hard steel up to diameters of 700 mm, with a length of 15 m to 30 m for tubes of 400 mm diameter.
Thanks to new electric welding systems, it could also return to the manufacture of welded tubes, now also with excellent mechanical performance and structural properties.
The method consists of two main phases: the production of perforated and rolling pilger.
In the production of hollow, solid steel bar (or ingot) it is heated in the oven and placed in a cylinder mill oblique. Here flows in the direction of the length between two cylinders arranged in an oblique way, that rotate in the same direction: the cylinders compress the bar and move it forwards.
The pressure of the cylinders creates, inside the bar, a longitudinal cavity which is made to slide a tip that the smooth and widens. This achieves the perforated steel, which has a much greater length of the bar (or ingot) initial and maintains a temperature high enough to be started to the second stage.
In the second phase, in drilled it is inserted a spindle, which pushes it between two cylinders rotating in opposite and overlapping each other. The cylinders pressing on drilled, exercising each round, a force not constant, composed of a phase of pressure that the perforated foil, followed by a phase inert.
Each complete turn of the two cylinders drilled advances, driven by the spindle. After the second phase the tube reaches a length from 5 to 10 times greater than the drilled departure. The outer diameter is determined by the distance between the rolling rolls; the inner one, the diameter of the mandrel.
More information: http://www.heatexchanging.com
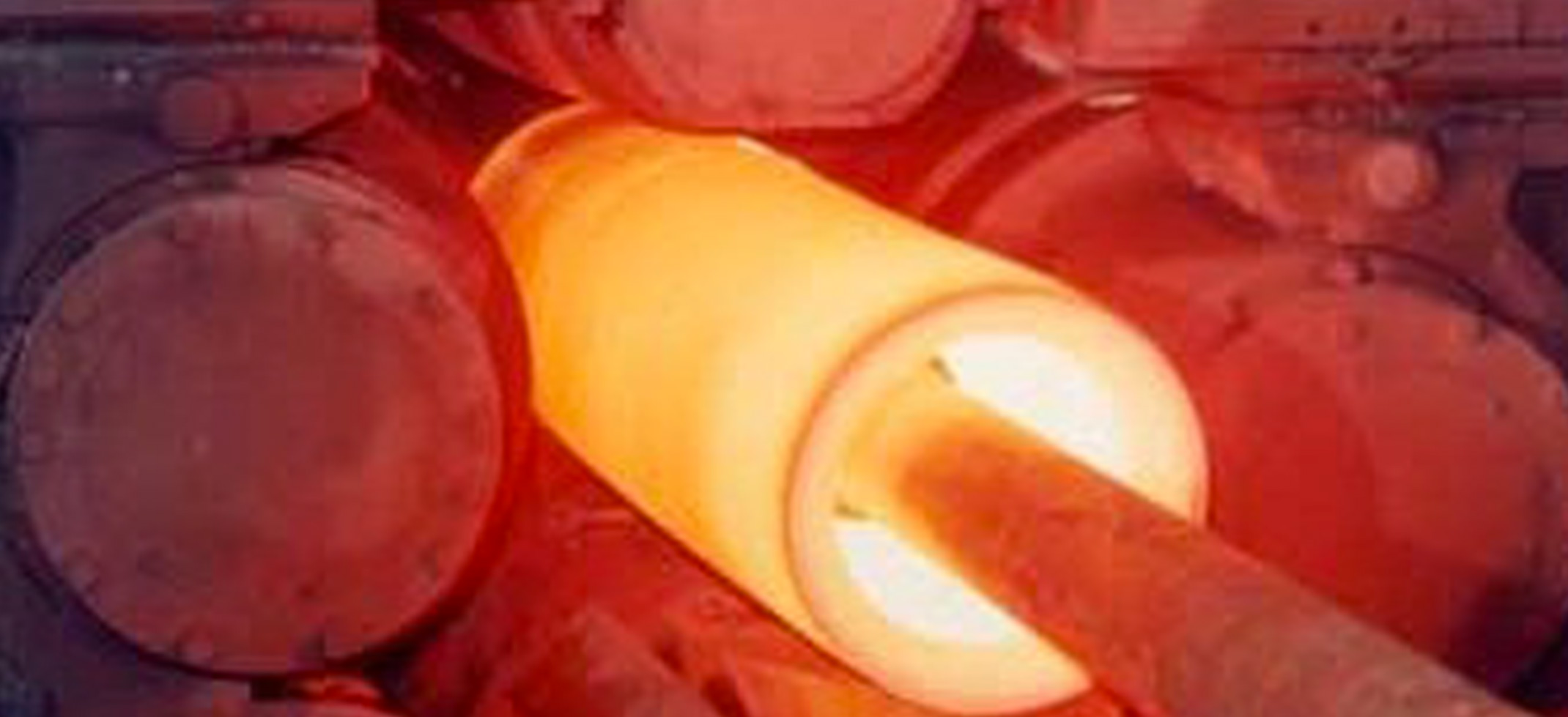