I componenti leggeri offrono all’industria aerospaziale e a quella automobilistica gli strumenti per ridurre il consumo di energia e le emissioni mediante lo sviluppo di veicoli meno pesanti, e forniscono ad altri settori industriali dei materiali flessibili per sviluppare nuovi strumenti innovativi. La fabbricazione di simili componenti leggeri di alta qualità ha tuttavia rappresentato spesso una sfida; vibrazioni e pressione durante il processo di fresatura spesso comportano il bisogno di un intervento manuale per finire la produzione, aumentando perciò i costi.
Il progetto DYNAMILL, completato lo scorso Ottobre, ha quindi cercato di sviluppare degli strumenti efficaci in termini di costo e sicuri per una produzione di massa di parti leggere a parete sottile ideali per settori con un buon potenziale di crescita nel mercato, come ad esempio quello del trasporto, della produzione di energia e della tecnologia medica.
Il risultato finale è rappresentato da una nuova piattaforma tecnologica che offre la pianificazione dell’intero processo, nuovi dispositivi adattivi di fissaggio e condizioni migliorate di taglio. Il controllo del processo è concentrato su elevato smorzamento e bassa eccitazione delle vibrazioni del pezzo in lavorazione, mentre la pianificazione è fortemente supportata da strumenti software all’avanguardia, inclusi modelli per simulazioni dinamiche dell’oscillazione oltre alla fabbricazione assistita dal computer.
I sistemi nuovi nel processo comprendono il fissaggio magnetico, e un dispositivo di fissaggio per la fabbricazione di grandi turbine. Complesse strutture a parete sottile sono state combinate con materiali ad alta resistenza, perfette per industrie con requisiti molto elevati per quanto riguarda sicurezza e qualità come ad esempio l’aviazione.
Maggiori informazioni: http://www.heatexchanging.it
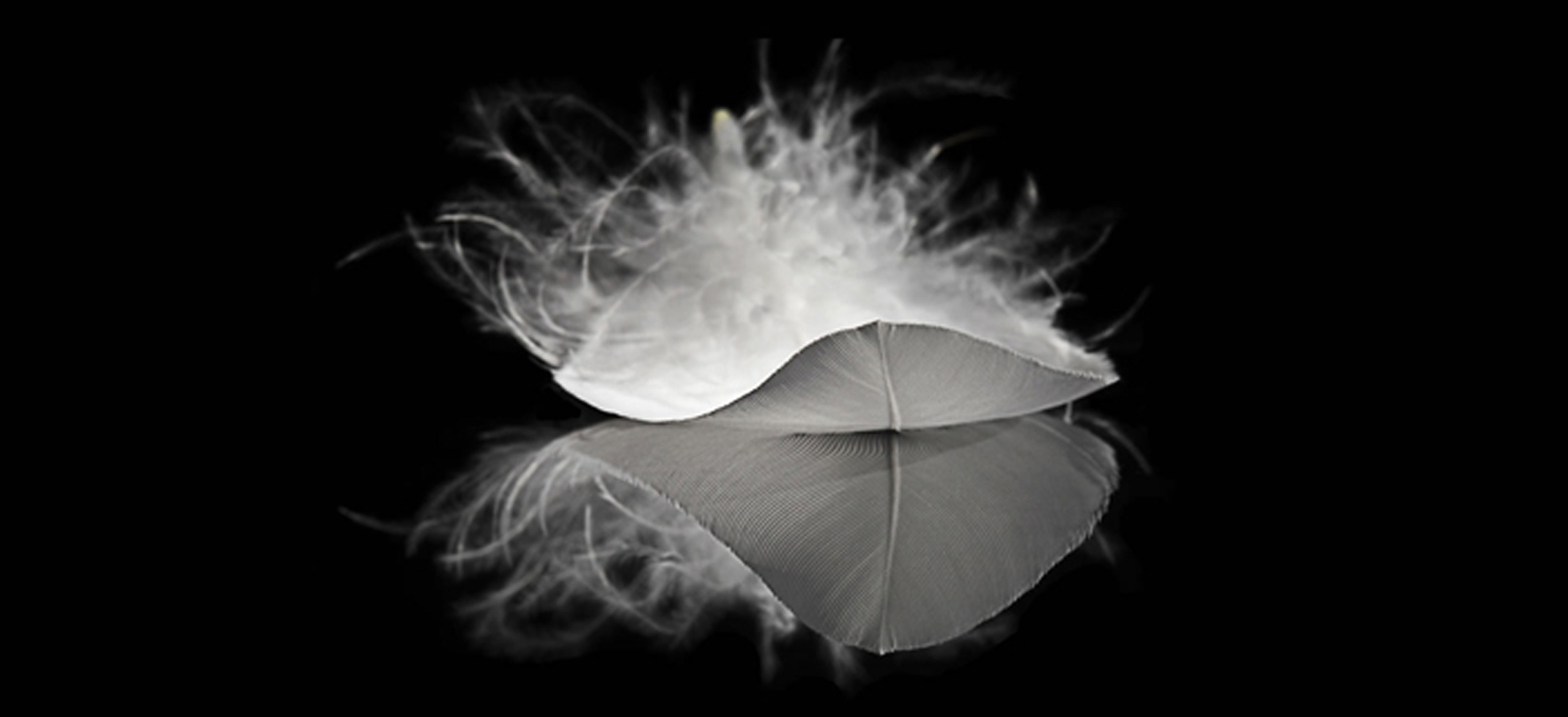